Unlocking the Magic of FDM 3D Printing: Discover the Secrets Behind Its Revolutionary Impact!
Fused Deposition Modeling, commonly referred to as FDM 3D printing, has emerged as a transformative force in modern manufacturing and technology. This innovative technique enables the creation of three-dimensional objects from digital files, making it accessible for both hobbyists and industrial applications. In this article, we aim to demystify FDM 3D printing, exploring its fundamental principles, applications across various industries, and the advantages and limitations associated with this technology. Whether you are a newcomer curious about 3D printing or a seasoned professional looking to enhance your knowledge, this guide will provide valuable insights into the world of FDM 3D printing.
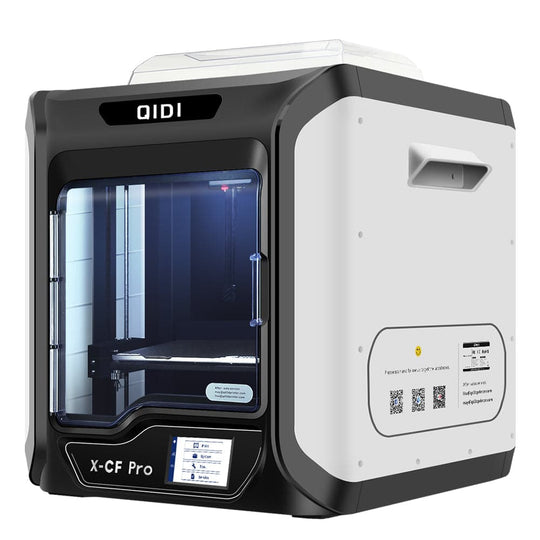
Understanding FDM 3D Printing
FDM 3D printing, developed in the 1980s by Scott Crump, is a widely used additive manufacturing process. The core principle of FDM is layer-by-layer construction, where materials are deposited sequentially to build an object from the ground up. The process begins with a digital model created using computer-aided design (CAD) software, which is then sliced into thin horizontal layers by slicing software. The printer's nozzle extrudes heated thermoplastic filament, which solidifies upon cooling to form each layer. This method allows for intricate designs and complex geometries that would be difficult or impossible to achieve with traditional manufacturing techniques. FDM has gained popularity due to its accessibility, affordability, and ease of use, making it a favorite among DIY enthusiasts and professionals alike.
Principles of FDM 3D Printing
The technical aspects of FDM printing revolve around the materials and the printing process itself. FDM primarily utilizes thermoplastics such as PLA (Polylactic Acid) and ABS (Acrylonitrile Butadiene Styrene). These materials are available in filament form, which is fed into the printer. The printer's nozzle heats the filament to a temperature where it becomes pliable, allowing it to be extruded in a controlled manner. The importance of design considerations cannot be overstated; a well-designed model ensures that the layers adhere properly and that the final product maintains structural integrity. Moreover, the printer's heating element plays a crucial role in maintaining the right temperature for both the nozzle and the build platform, preventing warping and ensuring a successful print. As my friend who is a mechanical engineer once said, "Understanding the nuances of material properties and printer settings can make or break your project."
Applications of FDM 3D Printing
FDM 3D printing finds applications across a wide range of industries, showcasing its versatility and potential. In aerospace, for instance, companies are utilizing FDM to produce lightweight prototypes and components that enhance fuel efficiency. The automotive industry benefits from rapid prototyping, allowing designers to test and iterate on parts quickly. In healthcare, FDM technology is used to create custom prosthetics and dental models tailored to individual patients, significantly improving patient outcomes. Education is another sector where FDM 3D printing is making waves; schools and universities are embracing the technology to teach students about design and engineering principles hands-on. I recall visiting a local university's engineering department, where students were building everything from drone components to architectural models, showcasing the practical applications of FDM technology in real-world scenarios.
Advantages and Limitations of FDM 3D Printing
The benefits of FDM 3D printing are numerous, making it a popular choice for various projects. One of its main advantages is cost-effectiveness; FDM printers are generally more affordable compared to other 3D printing technologies. Additionally, the speed of production is a significant factor, as parts can be printed relatively quickly, reducing lead times for projects. The versatility of FDM allows users to experiment with different materials and designs, fostering innovation. However, it is essential to acknowledge the limitations of this technology. Material restrictions can impact the strength and durability of printed parts, and print quality can vary based on factors such as printer settings and environmental conditions. My friend, who runs a small 3D printing business, often shares stories about overcoming these challenges, emphasizing the importance of knowledge and experience in achieving optimal results.
Key Insights on FDM 3D Printing
In summary, FDM 3D printing represents a significant advancement in manufacturing and design, with its layer-by-layer construction method enabling the creation of complex and customized objects. From its foundational principles to its diverse applications across industries, FDM technology is not only revolutionizing how we think about production but also empowering individuals and businesses to innovate. As we continue to explore the potential of 3D printing, it is evident that FDM will play a crucial role in shaping the future of technology, and we encourage readers to consider how they might harness this remarkable tool in their own projects or fields.